Paper Machine Clothing
As a specializing in paper machine clothing ( forming fabrics, press felts and dryer fabrics ) for paper machinery with over 15+ years of experience and an impressive market name, we are dedicated to delivering precisely match your unique requirements.
Selecting the right paper machine clothing, including forming fabric, press felt/press fabric, and dryer screen, is essential for the successful paper-making process. With a wealth of experience in this field, we have the knowledge and expertise to guide you in the selection process.
Our application experts are adept at crafting optimal solutions based on your specific needs, taking into account factors such as machine configurations in the forming and dryer sections, machine speed, pulp composition, paper types, grammage, and quality.
When it comes to technical support and maintenance, our experts-led team is here to provide you with professional insights and customized optimization solutions. We understand the importance of keeping your machinery running smoothly and efficiently.
Our technical sales experts are always ready to assist you. Whether you have questions about fabric specifications, technical details, or are seeking insights from our customer success stories, we have you covered. We also offer training sessions on various subjects, including safety and fabric applications.
At Sacsonss International we are committed to fostering a close partnership with you to ensure that your paper machine clothing is of the highest quality. Your success is our priority, and we look forward to collaborating with you to achieve excellence in paper manufacturing.
a) Forming Fabric
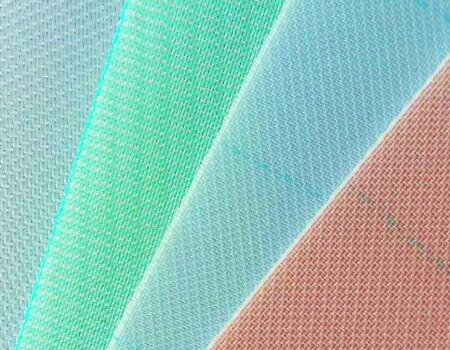
Forming fabric holds a critical position within the papermaking process as a key component of the paper machine. Its primary function is to facilitate the formation and dewatering of paper sheets. Specifically, it plays a pivotal role in removing water from the pulp suspension that flows from the headbox. This crucial step in the papermaking process is essential for achieving the desired paper quality and consistency. Therefore, selecting the appropriate forming fabric is essential to ensure the effective formation and dewatering of paper sheets during production.
- Single layer eight shaft
- Ten shaft 1.5 layer
- Double layer
- Two & half layer
- SSB (Triple layer)
Technical Specification of Forming Fabric
i) Single layer eight shed
8-shed single layer polyester forming fabric is the most wear-resisting one in the single layer screen, which has long performance life, but mesh print is relatively deep. It is mainly used for copying the paper-making bag, kraft paper, cardboard & corrugated paper, and so on.
ii) Ten shed 1.5 layer
1.5 Layer Forming Fabric is mainly used on the board, liner, brown paper and corrugated paper machine with machine speed 50m-400m/min, which have high air permeability as single layer forming fabric, and have a longer life than single layer forming fabric.
iii) Double layer
Double layer forming fabric is suitable for producing quality paper which includes printing paper, wrapping paper, board grade, onion-skin paper, newsprint. Suitable for medium and high-speed paper making machines.
iv) Two-and-half layer
2.5-layer forming fabric is one of our best-selling products, suitable for the production of Printing paper, Wrapping paper, Board grade, Onion-skin paper, Newsprint, and so on. Paper machines with speeds of 200-500 m/min.
v) SSB (Triple layer)
The Triple layer Forming fabric is the best for those who wants to retain as much fiber and faster drainage as possible. The increase with the count of the yarn ensures better support and retention while at the same time reduces the wire marks.
Triple-layer forming fabric is suitable for producing quality printing paper, tissue paper and cigarette paper, etc. Due to its excellent stability and resistant, it is ideal for high-speed paper machine.
b) Press Felts
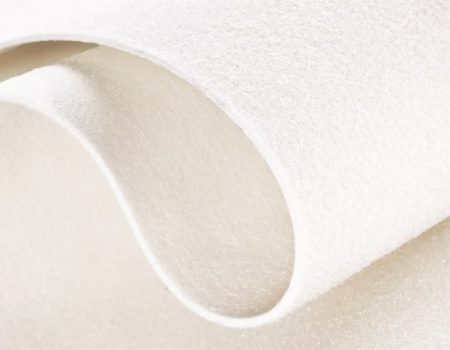
Press felts have a crucial role to play in the paper production process. They are instrumental in extracting moisture from the paper web post the forming section, all the while enhancing its smoothness and facilitating its journey to the dryer section. In order to fulfill this essential role, press felts are required to perform several key functions: water extraction, surface smoothing, and ensuring smooth and efficient paper transport. It's worth noting that with the advent of larger and faster paper machines in recent years, the demand for press felts of superior consistency and quality has seen a significant rise.
- 800 GSM to 2000 GSM Laminated Press felts.
- Paper making felts
Technical Specification of Press Felts
i) Single layer BOM press felt
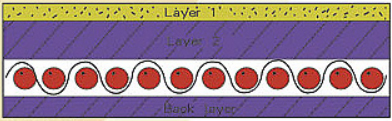
Single Layer BOM Felt is made up of single base layer mesh fabric and fiber layer. The base layer is woven from synthetic mono-filament or multi-filament. The fiber layer consists of the various lap of fiber web and different diameters of fiber for better drainage and fiber support index.
ii) Double layer press felt
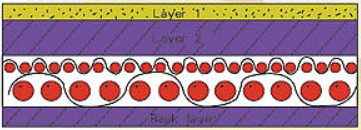
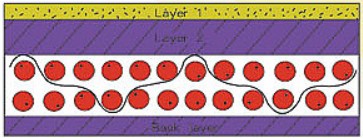
Double Layer Press Felts include a 1+1 composite structure and a double layer of MD yarn structure. The 1+1 composite structure consists of two-layer base meshes of different thicknesses.
Both of these base meshes can be changed in construction and sizes to suit the requirements of different paper machines.
Double layer felts have the features of high press resistance, good flexibility, permeability and size stability, less elongation, excellent tensile strength.
iii) Triple layer press felt
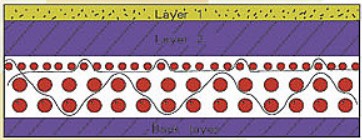
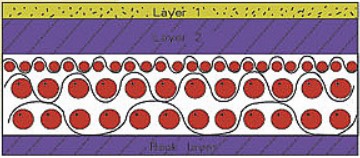
Three-layer BOM papermaking press felts include 1+2 composite, 2+1 composite and 1+1+1 composite three-layer BOM papermaking felts.
The press felt can adapt to the linear pressure above 200kN/m, has the characteristics of good elasticity, good water filtering performance, can effectively eliminate all kinds of marks, stable size, long service life and so on.
iv) Multilayer Press felts
Description
The base mesh layer of multi-axial laminated press felts is constructed from base meshes arranged in different directions and angles relative to the running direction of the felt.
According to the needs of the paper machine, the base mesh layer of the press felt can be superimposed into various forms such as 1+1 or 1+1+1, so that the warp and weft threads of the base mesh of each layer are not likely to be crushed by each other after overlapping. Multi-axial laminated press felts has more advantages, high resistance to high line pressure, faster speed increase and lower steam consumption.
Dryer Fabric
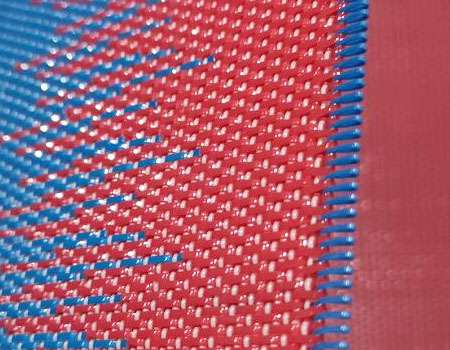
In the realm of papermaking, dryer fabric plays a dual role. Primarily, it acts as the agent responsible for extracting any residual moisture from the paper web that couldn't be eliminated through vacuum or pressing methods. Furthermore, it facilitates the bonding of fibers through the crucial process of hydrogen bonding.
Technical Specification of Dryer Fabric
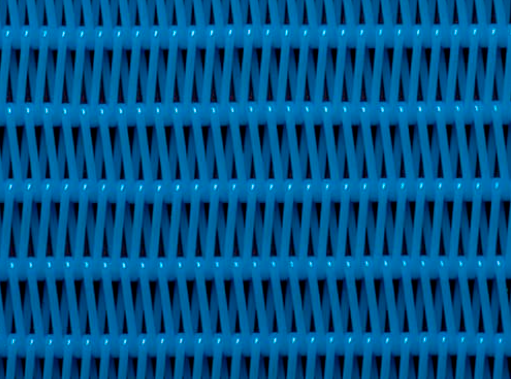
i) Spiral Link Dryer Fabric - 800 CFM to 1250 CFM
Spiral dryer fabric or screen is an endless construction comprising a plurality of spiral loops of monofilament yarns. The spiral loops are linked by a pin yarn inserted in the adjacent holes.
The specially designed spiral structure allows for rapid drainage, and superb distortion resistance and eliminates the need for conventional seams compared with the woven polyester dryer fabric.
The spiral dryer fabric is a specially engineered paper machine clothing for the drying sector in the paper mill, also widely deployed in many other industries like food drying, nonwoven conveying, printed textile drying, etc.
ii) Sludge Belt press fabric
Description
Polyester Spiral Press Filter Belts are made with spiral dryer fabrics with extra filler yarns inserted in the spiral loops to reduce the air permeability and less material loss on the surface of the fabric.
Polyester Spiral Press filter belts are usually made of abrasive resistant polyester.
Polyester Spiral Press Filter Belt is also a monofilament polyester fabric but not like a woven fabric, instead this is a polyester fabric with spiral twisted wires where pins hold the spirals together like a chain.
iii) Woven dryer screen
Woven dryer fabric influences the drying process by openness and contact area with the paper sheet. Different yarn structures and shapes are used to control air permeability (CFM) and influence properties such as contact area, wear resistance, stability and cleanliness.
Dryer fabrics are woven with round or flat monofilaments for drying requirements of different paper grades, and machine speeds. Flat wire dryer fabric is mainly used in the fore heating box of the drying zone, and also can be used for all the quality paper making.

Normally, the three-shed fabric is perfect for drying papers less than 70g and a four-shed one is ideal for those papers of weight larger than 70g. In addition, flat yarn woven polyester dryer fabric can be made to custom orders.
d) SS Diagonal mesh
5 mesh to 100 mesh in SS 316 L & SS 304.

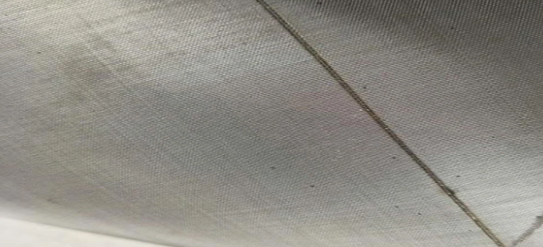